SEMINAR RÜSTZEIT-REDUKTION
SEMINAR-ZIELE:
- Kürzere Rüstzeiten
- Zeitgewinn von bis zu 50% bei der Durchlaufzeit
- Deutliche Reduktion der Losgrößen
- Erhebliche Verringerung von Ausschuss und Beständen
STILLSTAND STOPPEN – SO WEIT WIE MÖGLICH
Wie viele Stunden Ihrer täglich verfügbaren Arbeitszeit stellen die Maschinen Gutteile her – sprich Produkte, die Verkaufserlöse erzielen? Ganz gleich wie die Antwort lautet: es besteht fast immer „Luft nach oben“. Jeder unnötige Maschinen-Stillstand verschwendet wertvolle Zeit und verursacht erhebliche Kosten.
Rüstzeiten sind nicht generell vermeidbar: Es muss Material besorgt werden, es müssen Aufträge abgeholt oder Werkzeuge justiert werden. Rüstzeiten sind aber erheblich reduzierbar. Und das in jeder Branche – ob an der Abfüllanlage, der Stanz- oder Druckmaschine oder der Formteilproduktion.
In diesem Seminar lernen Sie die SMED-Methode kennen. Ihre Abkürzung steht für Single Minute Exchange of Die, das Umrüsten im einstelligen Minutenbereich. Diese Zielmarke klingt für viele Produktionen zunächst utopisch. Und oft sind viele Optimierungsmaßnahmen notwendig, um die einstellig-minutenschnelle Umrüstung zu erreichen. Doch hat die Praxis sehr vieler Unternehmen erwiesen, dass sie erreichbar ist. Die Zeitgewinne liegen am Ende oft deutlich über 50%. Und jeder einzelne, noch so kleine Optimierungsschritt erhöht die Produktivität.
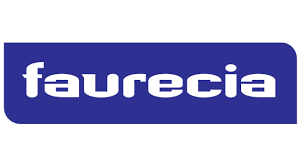
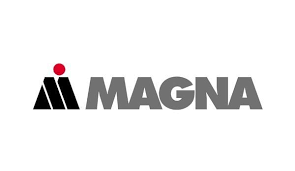
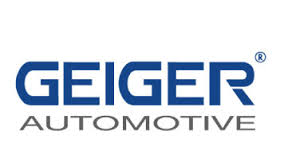
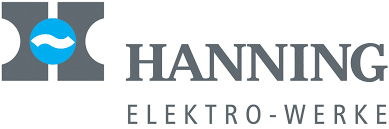
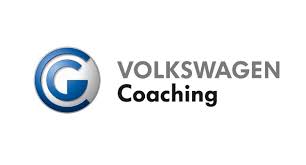
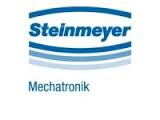
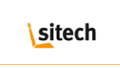
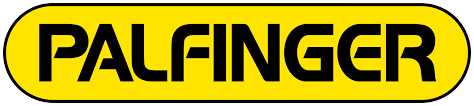
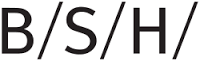
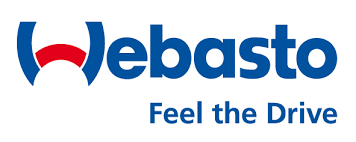
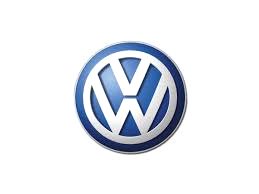
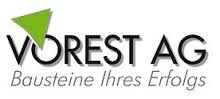
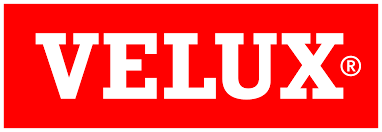

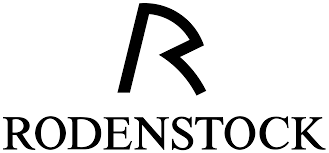
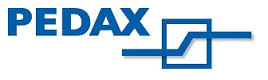
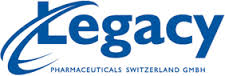
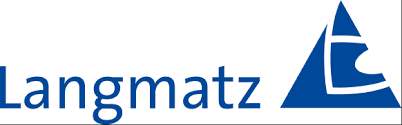
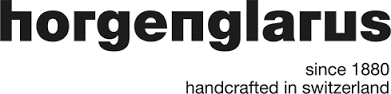
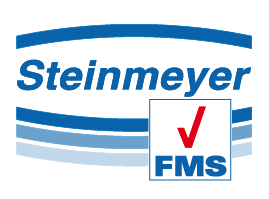
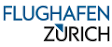
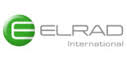

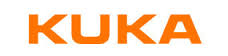
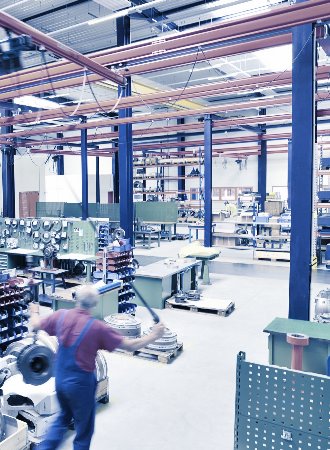
INHALTE SEMINAR:
THEORIE:
- Identifikation wertsteigernder, nichtwertsteigernder und kostensteigernder Tätigkeiten beim Rüstprozess
- Definition der Rüstparameter als Kriterien für Qualität und stabile Prozesse
- Unterscheidung Rüstzeit und Rüstaufwand
PRAXIS:
- Rüsttätigkeiten neu organisieren
- Maschinen-Einstellungen vereinfachen
- Arbeitsabläufe mit Maschinenlaufzeiten vereinfachen und beschleunigen
SEMINAR WERTSTROMDESIGN – MESSBARER NUTZEN FÜR UNSERE KUNDEN
Die Erfahrungen, die unsere Unternehmensberatung mit Wertstromdesign sammeln konnte, sind überzeugend. Durch die Visualisierung der Abläufe und Zusammenhänge können die Prozesse wesentlich schneller und gründlicher geprüft werden.
Die Material- und Informationsflüsse werden bei Anwendung dieses Verfahrens klar sichtbar. Schwachstellen im System werden sicher identifiziert, das Zusammenspiel der verschiedenen Abteilungen wird transparent. Mit diesem Kenntnisstand kann ein detaillierter Plan erarbeitet werden, der alle erforderlichen Maßnahmen enthält.
Wird die Optimierung der Prozesse auf diese Weise zielgerichtet vorangetrieben, sind schon nach kurzer Zeit Erfolge zu erkennen:
- Material- und Informationsflüsse werden transparent.
- Verbesserungspotentiale sind leichter zu identifizieren.
- Produktionsprozesse werden synchronisiert.
- Verkürzung der Durchlaufzeiten.
- Optimierung des Bestandes.